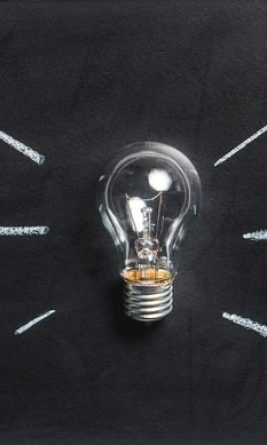
Logisch toch?
Wie in een productie-omgeving werkzaam is herkent wel dat een goed georganiseerde werkplek tijdwinst oplevert. Gereedschap dat je vaak gebruikt, dicht bij je werkplek. Een vaste plaats voor de opdrachten die wachten om geproduceerd te worden, vaste plaatsen voor transportmiddelen. Eigenlijk heel logisch allemaal. Vergelijk het maar met thuis. In je besteklade ligt doorgaans niet alle bestek kriskras door elkaar, maar gesorteerd in vakken van de bestekbak. Het zijn zaken waar je niet bij nadenkt, maar zo logisch zijn dat ze als vanzelfsprekend ervaren worden.
Moeilijker dan het lijkt
In de dagelijkse praktijk blijkt het goed organiseren van een werkplek moeilijker dan het in eerste instantie lijkt. Dat heeft te maken met verschillende aspecten. De hulpmiddelen kunnen ontbreken, waardoor het moeilijk wordt om geordend te werken, maar ook de discipline van de medewerker kan onvoldoende zijn om gestructureerd te werken. Bij werkplekken die door één medewerker worden bemand kan het zo georganiseerd zijn, dat hij of zij de spullen wel kan vinden, maar een buitenstaander niet. Reactie in de praktijk is vaak: ‘ik kan mijn spullen gewoon vinden, als ik ze opruim raak ik ze juist kwijt’. Dat is volgens mij niet waar omdat er ongemerkt veel zoektijd verloren gaat, die als ‘normale’ werktijd wordt beschouwd. Maar wat als je met twee of meer medewerkers op dezelfde werkplek werkt, bijvoorbeeld in ploegendienst? Als iedereen zijn eigen methode erop nahoudt, zorgt dat zeker voor verlies in tijd, laat staan de onderlinge irritatie die ontstaat.
5S werkplekorganisatie
Een goed georganiseerde werkplek is een uiting van samenwerken. Je hebt een gedeelde verantwoordelijkheid voor de werkplek en ieder heeft daarin zijn of haar taken. Goede samenwerking is een voorwaarde. Niets is zo lastig als samen de beste werkwijze bedenken én in stand te houden. Toch ligt daar de kracht van de zogenaamde 5S werkplekorganisatie. Een techniek die inmiddels bekend is in de Nederlandse maakindustrie. Ontstaan vanuit de LEAN filosofie en inmiddels een begrip. De vijf stappen zijn overzichtelijk; Scheiden(opruimen en overzicht creëren), Schikken(structureren van de gereedschappen, werkplekken en inzichtelijk maken van de routing), Schoonmaken(schoonmaken als dagelijkse routine en daarbij ook onderhoud en reparatie van kapotte spullen), Standaardiseren(afspraken visualiseren en vastleggen in de vorm van o.a belijning en werkinstructies) en de laatste en moeilijkste stap, stabiliseren(en verder blijven ontwikkelen). Het succes in de praktijk valt of staat met het samen uitvoeren en in stand houden. Het lijkt eenvoudig, maar heeft constante aandacht nodig. Het wisselen van banden van een Formule 1 auto is het ultieme voorbeeld van samenwerken en een georganiseerde werkplek. Anders is het wisselen van 4 banden in minder dan 2 seconden nooit haalbaar.
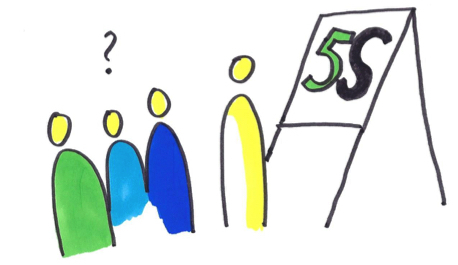
Ervaring uit de praktijk
In mijn dagelijkse praktijk kom ik mooie voorbeelden tegen. Zo ook bij een middelgrote Timmerfabriek. Hier was veel tijdsverlies in de productie omdat collega’s van elkaar gereedschappen leende en ‘vergaten’ terug te brengen. Het ging concreet om accuboormachines. Die waren er twee in het bedrijf en waren op minimaal 5 werkplekken nodig! Volgens de leiding waren de accuboormachines niet zo vaak nodig en zou niet iedereen tegelijkertijd ermee aan de slag zijn. Feitelijk wellicht juist. Alleen in de onderlinge samenwerking was dit een lastig aspect. De accuboormachines stonden nooit op de afgesproken plaats en werden ‘gehamsterd’. ‘Die heb ik direct toch weer nodig’. Best begrijpelijk, maar het leverde veel tijdsverlies op. Om dat inzichtelijk te maken heb ik een Multi Moment Opname gedaan om de effectieve tijd te meten. Het resultaat wat dat de tijdsbesteding aan orders slechts 40% was van de beschikbare tijd van een medewerker. Natuurlijk kun je niet 100% effectief zijn en zal er transport nodig zijn, soms overleg en zijn er storingen. Maar zo veel? Met de groep zijn we gaan onderzoeken op de werkvloer. We kwamen samen al snel tot de conclusie dat gereedschappen niet op een logische en zelfde plaats lagen. Met andere woorden: veel zoekwerk en frustraties. We ontdekten ook dat er van bepaalde gereedschappen tekorten waren, waardoor het ‘lenen zonder terugbrengen’ in de hand werd gewerkt. Wat nu?
Twee concrete acties: 1. inventarisatie van benodigde gereedschappen per werkplek ten opzichte van het aanwezige gereedschap. 2. een opbergplaats en ruimte voor de gereedschappen.
De gereedschappen zijn aangeschaft nadat de tekorten zijn geïnventariseerd. Voor de opbergplaats heeft de groep zelf een ontwerp en een gereedschapskar gemaakt. Over de plaats was discussie, totdat iemand met het goede idee kwam om een gereedschapskar op wielen te maken.
Nadat deze gereedschapskarren en nieuwe gereedschappen in gebruik waren genomen, is na enkele maanden een nieuwe Multi Moment Opname gedaan. Het resultaat was op zijn minst opmerkelijk. De tijdsbesteding effectief aan orders was gestegen naar 60%! Het was vooral opmerkelijk omdat in een rondje langs de medewerkers de indruk werd gewekt dat het prettiger werkte, maar voor hun gevoel niet meer werd geproduceerd. Na verder onderzoek bleek dat het aantal overuren drastisch was afgenomen. De output werd gemaakt in de reguliere uren. Een jaarlijkse besparing van enkele tienduizenden euro’s.
Toen we samen de resultaten bespraken, werd de conclusie getrokken dat het opgeruimd veel lekkerder werkt! De output is per gewerkt uur hoger dan voorheen en onderlinge samenwerking verliep veel soepeler. Die ervaring en constatering geeft de motivatie om dit ook vol te houden met elkaar.
Samen bedenken, samen uitvoeren en samenwerken zijn de succesfactoren bij 5S werkplekorganisatie.
Neem gerust contact met ons op, daar word je altijd wijzer van!
Stuur een bericht via onze contactpagina of bel 06-51 38 15 50.