Operational Excellence
Werken naar Operational Excellence in een organisatie kenmerkt zich door het continu verbeteren van operationele processen door systematisch te focussen op klantwaarde, processtappen en activiteiten die geen waarde toevoegen voor de klant te beperken of te elimineren. Het benutten van de kennis en vaardigheden van medewerkers en effectieve toepassing van technologie en vernieuwingen om daarmee een hogere productiviteit te realiseren (effectiever in dezelfde tijd) die leidt tot een betrouwbaarder en voorspelbaarder proces. Praktische strategieën om Operational Excellence te realiseren zijn Quick Response Manufacturing (voor maakbedrijven met kleine (klantgerichte) series met veel variatie) en LEAN Manufacturing (voor maakbedrijven met grotere series in minder varianten).
Quick Response Manufacturing (QRM)
QRM is een organisatiebrede strategie om sneller te reageren op de veranderingen in de klantvraag door het (extreem) verkorten van doorlooptijden. QRM is uitermate geschikt als strategie in organisaties waar kleine volumes verwerkt worden met hoge variatie. QRM kent 4 speerpunten waarmee aan de slag wordt gegaan: Tijddenken, Anders Organiseren, Systeemdynamica en Organisatiebrede aanpak. Hieronder leggen we deze en andere termen graag verder aan je uit.
-
Tijddenken (in plaats van kostendenken)
Lees meer
Doorlooptijden bestaan voor het grootste gedeelte uit de wachttijd van een opdracht, order of project. Als er tijdsdruk ontstaat wordt eerst gedacht aan het versnellen van de processen en wordt wachttijd tussen de processen over het hoofd gezien. Juist daar is de grootste winst te behalen om doorlooptijden te verkorten. Gemiddeld genomen ligt een order of project in de organisatie meer dan 85% van de tijd te wachten. En wachten kost ook geld...
-
Anders organiseren (van sturing naar zelfsturing)
Lees meer
Veruit de meeste organisaties zijn georganiseerd zoals het leger. Boven in de organisatie de admiraal (de directeur) en daaronder de generaals (managers) die de operatie aansturen. In deze wijze van organiseren zijn vele denkbeeldige muren en barrières om snel te kunnen handelen in de operatie. Een vraag van een soldaat, moet via de sergeant naar de majoor en zo verder. Wat mag de soldaat zelf besluiten? Zo werkt het in organisaties ook nog vaak. Wat mag een medewerker zelf besluiten? Zelfsturing en het werken in teams of ‘cellen’ doorbreekt de ‘oude’ structuur. Door het proces in te richten om de doorlooptijd van opdrachten en projecten zo kort mogelijk te maken, is het samenwerken tussen verschillende functionarissen essentieel. Door een team in te richten om de noodzakelijke taken uit te voeren ontstaat een model waarin de klantvraag centraal komt te liggen.
-
Systeemdynamica (snelheid in processen)
Lees meer
Als je snel van A naar B wilt, moet je kunnen doorrijden in het verkeer. Files vertragen de reistijd (en veroorzaken frustraties). Het ontstaan van files is te verklaren door te veel auto’s op hetzelfde stuk weg, op hetzelfde tijdstip. De oorzaken kunnen verschillend zijn. Het kan liggen aan een ongeluk waardoor de weg is versperd, maar vaak is het teveel tegelijkertijd. En de toestroom blijft maar komen. In het verkeer zijn er methoden in het leven geroepen om dit te verbeteren, zoals toeritdosering en de spitsstrook. Maar als er een ambulance komt, krijgt deze altijd voorrang. Dan vertraagt de rest van het verkeer weer. In organisaties is het net zo. Als de beschikbare capaciteit te vol wordt gepland, ontstaat er file in orders of projecten. Dat heeft te maken met ons denken in kosten. Een machine of bewerking die niet productief is, kost geld. Maar het kost pas echt geld als er door het vastlopen van de doorstroming minder orders uitgeleverd worden. Dan kan er ook geen factuur verstuurd worden. Het bevorderen van de doorstroming van orders en projecten vraagt om vrije ruimte. Alleen dan is het mogelijk om snelheid te maken!
-
Organisatiebrede aanpak (iedereen in de organisatie doet mee)
Lees meer
De manier van werken met QRM verandert, onder meer door zelfsturing en door te kijken naar het totale proces in plaats van te letten op deelprocessen. Die interactie vraagt om ieders betrokkenheid. Dat vraagt ook openheid, inzicht en invloed van medewerkers. ‘Dat is niet mijn taak’, is niet meer aan de orde. Samenwerken met elkaar is de succesfactor. Dat vraagt nogal wat van een organisatie en al haar medewerkers. Het betekent elkaars taken over kunnen nemen (crosstrainen), blijven leren en met elkaar de klantvraag centraal blijven stellen. De rol van de leiding verandert van sturend naar ondersteunend. Het is een misvatting dat er geen leiding meer nodig is. Meer dan ooit is leiderschap nodig om tot een succesvolle invoering van QRM te komen. Maar het spelen van het ‘baasje’ werkt niet meer. Het vraagt een andere wijze van leiderschap, gebaseerd op gelijkwaardigheid, delen van kennis en kunde en samenwerken.
-
Agile
lees meer
Agile is een aanpak waarbij flexibiliteit en wendbaarheid centraal staan omdat de omstandigheden continue kunnen veranderen. Bij Agile werken staat projectmatig werken centraal. Door Agile te werken (en te leiden) gaan we weer terug naar de basis: focus op de klant, de medewerkers en het gewenste eindresultaat.
Beweeglijk en lenig, dat zijn de letterlijke vertalingen van Agile. In moderne bedrijven wordt steeds meer projectmatig gewerkt. Soms zelfs helemaal. En vaak met groot succes.
Agile breekt grote projecten op in korte periodes (sprints) van 2 tot 4 weken. Iedere sprint is een klein op zichzelf staand project. Door deze manier van werken ben je flexibel en wendbaar, maak je meer snelheid, loop je minder financiële risico’s, zijn alle betrokkenen continue aangesloten en lever je na iedere sprint concrete deelresultaten op.
Is Agile altijd toepasbaar? Nee, voor repeterende en procesmatige werkzaamheden is Agile minder geschikt. Voor alle overige werkzaamheden, is de Agile-aanpak vaak passend. De capaciteiten en de veranderingsbereidheid van medewerkers en management zijn cruciaal. Agile-teams zijn zelfstandig, zelfsturend en zeer resultaatgericht.
-
Lean Manufacturing
Lees meer
Lean manufacturing is een methode om bedrijfsprocessen gericht te verbeteren. De methode concentreert zich op het reduceren van verspillingen.
Lean manufacturing onderscheidt zeven categorieën van verspilling: overproductie, voorraden, fabricagefouten, fabricageverstoringen, wachttijden, transport en onnodige (zoek)bewegingen.
Deze ‘bronnen van verspilling’ worden opgespoord via value stream mapping. Dat houdt in dat middels een stroomdiagram in kaart wordt gebracht welke bedrijfsprocessen waarde toevoegen en welke niet.
Het doel van lean manufacturing is vervolgens, om de ‘waardestroom’ zo groot mogelijk te maken. Om dat voor elkaar te krijgen wordt (naar keuze) gebruik gemaakt van diverse productieconcepten die in de twintigste eeuw zijn ontwikkeld, zoals just-in-time productie, Kanban, cellular manufacturing, visual manufacturing.De oorsprong van Lean Manufacturing ligt in Japan, bij Toyota. In de vijftiger jaren bedacht werkplaatschef Taiichi Ohno dat alleen bedrijfsprocessen die waarde creëren voor de klant, nuttig zijn. Hiermee legde hij de kiem voor het Toyota Productiesysteem. Later werd LM verder ontwikkeld en gepromoot door James P. Womack en Daniel Jones van het Massachusetts Institute of Technology (MIT) in de VS.
-
5S werkplekorganisatie
Lees meer
5S is een methode, gericht op het verbeteren van de organisatie, met de werkplek als uitgangspunt. Door die te optimaliseren worden verspillingen voorkomen en wordt de basis gelegd voor hogere kwaliteit in de uitvoering van de dagelijkse processen.
S1: Scheiden
Scheiden of opruimen betekent hier onderscheid maken tussen wat noodzakelijk en wat overbodig is. Het onnodige moet verdwijnen. Dat zijn onder andere kapotte of beschadigde voorwerpen, voorwerpen die lang niet meer gebruikt of onveilig zijn. Het risico op vallen, struikelen, stoten, beschadigen en verwonden vermindert aanzienlijk en de doorgangen worden ruimer. Een praktisch systeem om voorwerpen te scheiden, is om naar alle aanwezige voorwerpen te kijken en zich af te vragen waarom dit voorwerp hier is. Als het onduidelijk is krijgt een voorwerp een rode kaart met daarop de vraag wat er met het voorwerp moet gebeuren. Een criterium hiervoor kan de gebruiksfrequentie zijn: hou enkel die zaken aanwezig op de werkplek die nodig zijn voor de productie van de komende week. Bij het scheiden wordt met de verschillende gebruiksfrequenties rekening gehouden. De 5S-begeleider stelt de vragen en doet voorstellen, maar de werknemer/gebruiker beslist uiteindelijk zelf.S2: Schikken
Schikken betekent de gereedschappen een vaste plek geven, de werkplek zodanig organiseren dat iedereen alles snel en gemakkelijk kan vinden: een geschikte plaats voor alles en alles op zijn geschikte plaats. Hierbij wordt rekening gehouden met ergonomie en hygiëne. Alles binnen handbereik bijvoorbeeld.S3: Schoonmaken
Schoonmaken betekent het reinigen van muren, vloeren en alle machines, gebruiksvoorwerpen, opbergsystemen enz. Ook het voorkomen van verontreiniging door het elimineren van oorzaken van storingen en incidenten, zoals het uitschakelen van vervuilingsbronnen. Het is ook het vastleggen van schoonmaakmethodes, standaarden en verantwoordelijkheden, regels en normen opstellen. Schoonmaken verhoogt de veiligheid en vermindert de kans op afkeur. Ook is schoonmaken een hulpmiddel om de machine in optimale staat te houden. De gevonden afwijkingen kunnen worden doorgegeven aan de desbetreffende afdeling/persoon en tijdens het preventieve onderhoud worden vervangen of hersteld.S4: Standaardiseren
Standaardiseren geeft duurzaamheid aan de eerste drie stappen. De eerste drie S'en worden een gewoonte door methodes in te voeren die deze eerste fases vastleggen. Enkele methodes zijn: visuele hulpmiddelen gebruiken (afbakening met lijnen, kleuren etc.), iedereen kent het wie, wat, waarom, hoe van de werkplaats, de betrokkenen kunnen snel een onderscheid maken tussen normaal en abnormaal. Onvoorziene omstandigheden brengen risico's met zich mee. Door gestandaardiseerde procedures zijn die verrassingen tot een minimum beperkt.S5: Standhouden of systematiseren
Systematiseren betekent het borgen van de andere vier pijlers, de zorg voor behoud en continuïteit, het altijd volgen van de gestandaardiseerde procedures. Hulpmiddelen zijn controlelijsten of audits op orde en netheid. De auditresultaten kunnen bekendgemaakt worden via tabellen of figuren en persoonlijke of themadoelstellingen kunnen afgesproken worden zodat een regelmatige evaluatie van deze scores mogelijk is.
Manufacturing Critical path-Time (MCT)
Een representatieve hoeveelheid kalendertijd vanaf het moment waarop een klant een order geeft, het kritieke pad volgend tot aan de eerste (deel)levering van de order of opdracht aan een afnemer.
MCT is het meetinstrument voor de analyse van processen om snel en eenvoudig te bepalen waar de grootste besparingen te realiseren zijn in wachttijden.
QRM cel
Het geheel van een aantal multifunctionele bronnen (mensen en/of machines). Zo samengesteld dat de bronnen de achtereenvolgende bewerkingen compleet kunnen uitvoeren, voor de gekozen Focus Target Market Segment. Dit is het deel van de organisatie waar met doorlooptijdreductie de meeste impact bereikt kan worden voor klanten.
Flow
De mate van doorstroming van orders of opdrachten in een organisatie. De meetfactor is de MCT.
Semco Style
Industriële democratie en corporate re-engineering
Semco Style zag het licht in 1980, toen de 21-jarige Ricardo Semler de Semco Group, fabrikant van industriële mixers en pompen, van zijn vader overnam. Op zijn eerste werkdag ontsloeg hij 60 procent van alle topmanagers. Daarop bleef hij het bedrijf democratiseren en zette hij de bedrijfshiërarchie op z’n kop door zoveel mogelijk beslissingsvermogen aan het personeel over te dragen.
Van 4 naar 212 miljoen
In 20 jaar tijd breidde Semco het personeelsbestand uit van 90 naar 3.000 werknemers en zorgde voor een groei van de jaaromzet van 4 miljoen naar 212 miljoen dollar, bij een personeelsverloop van slechts 2%. De Semco Group heeft zich inmiddels ontwikkeld tot Semco Partners, dat buitenlandse bedrijven helpt om hun vleugels uit te slaan naar de Braziliaanse markt. Semco Partners hanteert hiervoor een geavanceerd joint-venturemodel dat de Semco Style managementpraktijken combineert met de expertise en het productaanbod van partners.
Effectiever, winstgevender en flexibeler
De toepassing van Semco Style binnen de nieuwe bedrijven heeft geresulteerd in een interne-opbrengstvoet (IRR) van 46,5%. Het bewijs dat bedrijven die Semco Style toepassen effectiever, winstgevender en flexibeler zijn en kunnen bogen op een hogere klantentevredenheid en gelukkiger collega’s.
Vijf sleutelprincipes
In de loop der jaren heeft Semler zijn managementaanpak verfijnd en versterkt met een theoretische basis. Dit heeft geresulteerd in de Semco Style organisatiemethodiek. Semco Style is gebaseerd op vijf sleutelprincipes die de basis vormen van circa 30 managementprogramma’s en ruim 100 krachtige bedrijfspraktijken. Dit zijn:
- Vertrouwen
- Reductie van controle
- Zelfmanagement
- Extreme stakeholder alignment
- Creatieve innovatie
Vallen en opstaan
Deze sleutelprincipes omvatten veel meer dan zelfbestuur. En ze zijn onderling afhankelijk: als één principe uit de optelsom wordt verwijderd, verliezen de andere principes aan relevantie. Semco Style is geen recept dat je klakkeloos moet volgen of een onwrikbaar dogma. Semco Style is het resultaat van vallen en opstaan, van een paar stappen vooruit doen en een paar stappen terug. Het is bedoeld om voor onbepaalde tijd werk in uitvoering te blijven.
Bron: semcostyle.org/nl/over-ons-2
-
Supply cain
Lees meer
Het totale pakket van activiteiten van grondstof tot eindproduct (incl. het proces van informatie, materiaal en financiën). De Supply Chain bestaat uit drie fases:
Fysieke stroomManufacturing Critical path-Time (MCT)
Productie stroom
Controle stroom (financiële/ administratieve stroom) -
Engineer-to-order (ETO)
Lees meer
Deze productievorm gaat uit van klantspecifieke productie en vraagt maatwerk. Het produceren van de producten begint niet voor een klantorder is gearriveerd.
-
Make-to-order (MTO)
Lees meer
Bij deze productievorm worden producten pas geproduceerd als orders arriveren. Echter, is dit een combinatie van maatwerk en standaard onderdelen. De productie bestaat uit een groot assortiment eindproducten, gecreëerd van relatief weinig grondstoffen. Bijvoorbeeld staal, één grondstof maar vele mogelijkheden tot eindproducten. De klant is bereid te wachten voor exclusiviteit. Een goed voorbeeld van een make-to-order product is zeilboten, een combinatie van maatwerk en standaard onderdelen.
-
Assemble-to-order (ATO)
Lees meer
Bij deze productievorm wordt maatwerk geproduceerd uit basiscomponenten of halffabricaten. De basiscomponenten of halffabricaten liggen vooraf op voorraad en worden gefabriceerd tot een eindproduct bij een klantorder. Voorbeeld hiervan is de auto-industrie. Het lijkt erg op make-to-order, echter zijn er meer halffabricaten in het spel, inclusief meer voorraad.
-
Make-to-stock (MTS)
Lees meer
Bij deze productievorm wordt uitgegaan van een hoog volume van standaardproducten. Het bedrijf produceert in batches en op voorraad, nog voordat klantorders arriveren. Een make-to-order omgeving gaat vaak uit van flow productie, er zijn meer grondstoffen dan eindproducten (bijvoorbeeld: balpennen, lampen etc.)
-
Massa maatwerk
Lees meer
Bij deze productievorm wordt uitgegaan van een hoog volume van standaardproducten. Het bedrijf produceert in batches en op voorraad, nog voordat klantorders arriveren. Een make-to-order omgeving gaat vaak uit van flow productie, er zijn meer grondstoffen dan eindproducten (bijvoorbeeld: balpennen, lampen etc.).
-
Productlevenscyclus
Lees meer
De bovenstaand beschreven productievormen kunnen gerelateerd worden aan de productlevenscyclus. Afhankelijk van de fase (en de exclusiviteit) waarin het product zich bevindt wordt de productievorm gekozen.
Introductie: ETO
Groei: MTO/ ATO
Volwassenheid: MTS
Terugval: MTO -
Klant Order Ontkoppel Punt (KOOP)
Lees meer
Het klantenorderontkoppelpunt (KOOP) is in de marketing en de logistiek het punt dat aangeeft hoe ver stroomopwaarts in een bedrijfskolom de klantenorder doordringt in het productie- of het distributieproces, van een aanbieder van een product of dienst. Het wordt ook wel het hoofdvoorraadpunt genoemd. Het KOOP is een concept waarmee de onderneming vast kan stellen op welke plaatsen in de goederenstroom voorraden nodig zijn zonder dat de logistieke servicegraad wordt aangetast. KOOP is oorspronkelijk beschreven door Hoekstra en Romme op basis van ervaringen bij Philips.
De ligging van het KOOP is dus sterk afhankelijk van de logistieke grondvorm of het logistieke concept van een bedrijf of bedrijfskolom. Het deel van het proces dat voor het KOOP ligt, wordt niet door een klantenorder aangestuurd. Planning en uitvoering van dit deel dienen op verwachtingen van de toekomstige klantvraag (forecast) te gebeuren. Het deel van het proces dat na het KOOP ligt, wordt wel aangestuurd door een klantenorder.
Vijf plaatsen waar het klantenorderontkoppelpunt (KOOP) kan liggen:
Ter illustratie van de verschillende ontkoppelpunten zijn hier enkele voorbeelden opgenomen.
OP1 Maken en verzenden uit lokale voorraad
De organisatie produceert op eigen risico en stuurt de producten naar de 'nog niet'-afnemers. Standaardproducten met een relatief korte leveringstijd. (levensmiddelen).
OP2 Maken voor centrale voorraad
De organisatie produceert en legt de producten op voorraad. Dure duurzame standaardproducten (duurzame verbruiksgoederen zoals koelkasten, wasmachines, enzovoort).
OP3 Assembleren op order
De organisatie houdt de componenten van het product op voorraad en assembleert deze op afnemersspecificatie. Modulaire hoofdcomponenten (computerbedrijf, productie van auto's).
OP4 Maken op order
De organisatie heeft grondstoffen en materialen op voorraad en produceert op afnemerspecificatie. Grondstoffen en onderdelen (meubelbranche en grafische drukwerk).
OP5 Inkopen en maken op bestelling
De productie heeft veelal een projectmatig karakter. Geen voorraden, eventueel afroepcontracten (scheepsbouw).
In één organisatie kunnen diverse producten en / of afnemersgroepen diverse ontkoppelpunten voorkomen, afhankelijk van de karakteristieken van deze producten en van afnemers.
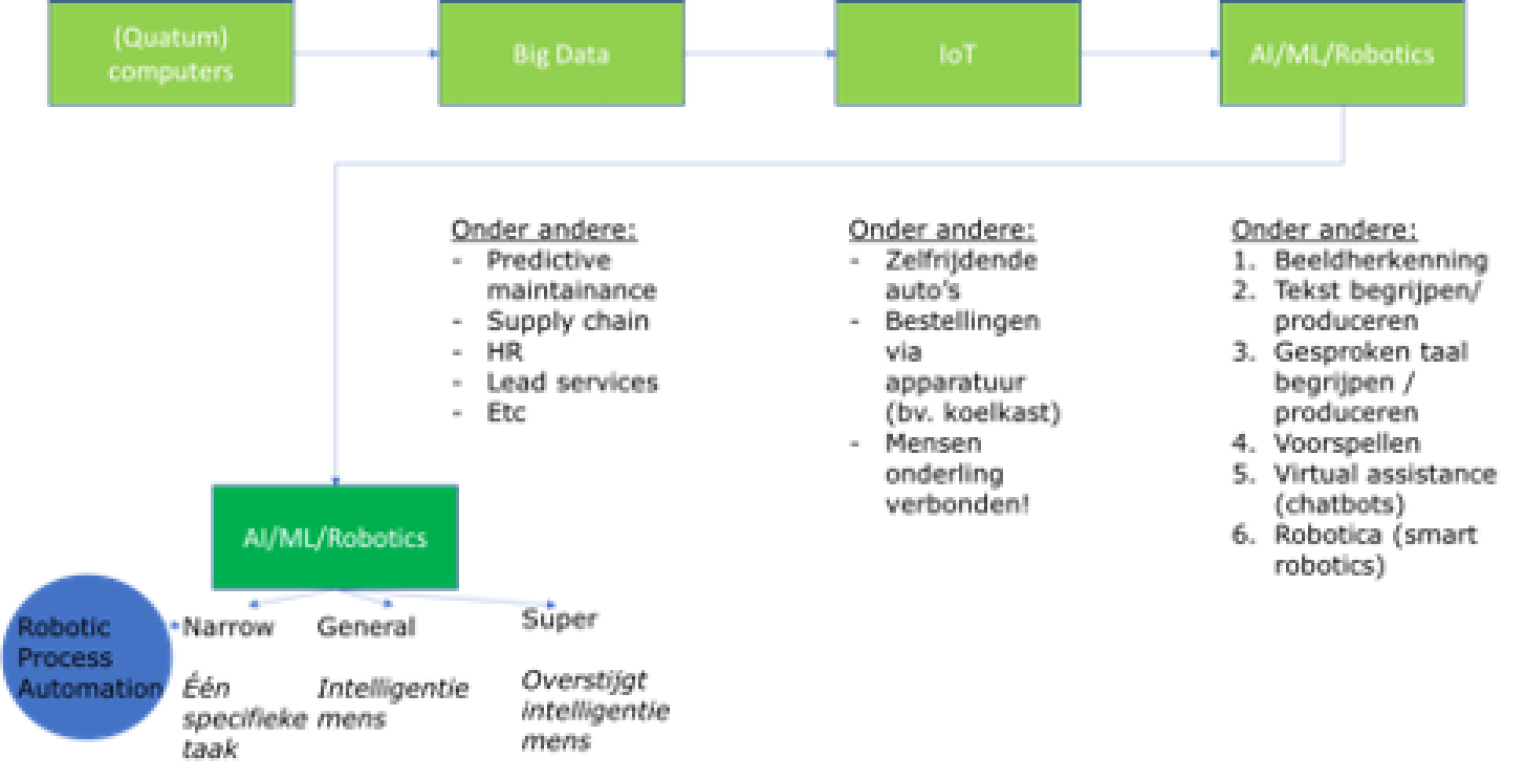
-
Speelveld digitalisering, big data, Internet of Things Artificial Intelligence en Robotics
Lees meer
Big Data
Men spreekt van big data wanneer je werkt met een of meer datasets die te groot zijn om met reguliere database managementsystemen onderhouden te worden. Big data spelen een steeds grotere rol. De hoeveelheid data die opgeslagen wordt, groeit exponentieel. Ook het analyseren van deze data speelt een steeds grotere rol.Internet of Things
Het ‘Internet der dingen’ (Nederlandse vertaling) is een voorgestelde ontwikkeling van het internet, waarbij alledaagse voorwerpen verbonden zijn met een netwerk en via dat netwerk gegevens kunnen uitwisselen. Men gaat er van uit dat de door mensen bediende computers – zoals desktops, tablets en smartphones – op een dag in de minderheid zullen zijn op het internet. De mogelijkheden die ontstaan wanneer fysieke objecten en de virtuele wereld samenkomen is het belangrijkste aspect van het internet der dingen. “Slimme” objecten spelen hierbij een sleutelrol: met gebruik van sensoren kunnen deze objecten de omgeving in zich opnemen en via ingebedde netwerktechnologie kunnen ze met elkaar communiceren, gebruik maken van internetdiensten en interactief communiceren met mensen. De “dingen” in de term de internet der dingen zijn dus allemaal zelf computers die via het internet zaken monitoren en regelen.Artificial Intelligence (AI)
Binnen AI kan onderscheid gemaakt worden tussen "sterke AI" en "zwakke AI".Sterke AI houdt zich bezig met onderzoek met betrekking tot het creëren van een computer of software die echt kan redeneren en problemen kan oplossen, en die wellicht zelfbewustzijn zou hebben; hiervan zijn weer twee subtypen te onderscheiden. De mens-gelijke AI (General), een computer die redeneert en denkt als een mens. En de niet-mens-gelijke AI, waarin de computer een niet-menselijke, maar eigen computer-intelligentie ontwikkelt (Super).
Zwakke AI houdt zich bezig met onderzoek in beperkte deelgebieden waarin gedragingen mogelijk zijn die intelligent lijken, maar niet echt intelligent zijn. Hier zijn de meeste vorderingen gemaakt, in de vorm van bijvoorbeeld zoekalgoritmen en expertsystemen (Narrow).
RPA (Robotic Process Automation)
Is een techniek die gebruikt wordt voor het automatiseren van bedrijfsprocessen, met behulp van zogenaamde 'software-robots'. Het is gericht op het automatiseren via de user interface, door het handmatige proces na te bootsen. Hoewel het begrip anders kan suggereren, komen er geen daadwerkelijke fysieke robots aan te pas.De term 'robot' slaat op het idee dat het software processen uitvoert zoals een mens dat zou doen. Hierdoor kan gesproken worden van virtuele werknemers. De software-robots kunnen bijvoorbeeld op knoppen klikken, informatie in tekstvelden schrijven en bestanden openen, lezen en bewerken. Een robot heeft zijn eigen (virtuele) werkstation en kan ook maar één proces tegelijk uitvoeren.
Inmiddels zijn er verschillende manieren waarop verder opschalen mogelijk wordt. Zo kunnen bij de meeste grote aanbieders robots op afstand aangestuurd worden, waardoor er een digitale 'workforce' gecreëerd kan worden van tot wel 10.000 robots. Die voeren op hun eigen werkstation processen uit, terwijl de menselijke gebruiker het overzicht kan houden.